Hot Air Airship Projects
Similar to Helium Airships, Hot Air Airships have about 1/3 of the lift capability of Hydrogen or Helium
requiring their size to be much larger for the same take-off weight compared to their cousins.
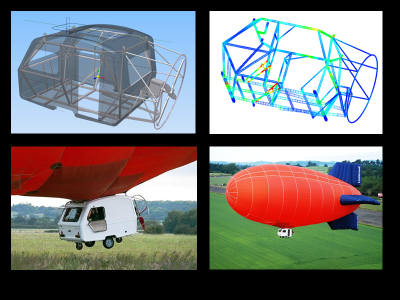
The pictures on the left illustrate a typical type of project that Aeromechanics Ltd thrives on. The end user (in this case a globally known TV production organisation that present an automotive show) have a one-off idea that requires both design and certification in a very compressed time frame and budget.
Top left: CAD files produced by the design team are forwarded electronically to Aeromechanics for adapting the surface/solids data to an appropriate form for the Finite Element analysis tools.
Top right: Aeromechanics provides regular structural feedback during the modelling and analysis phases of the project. This promotes the ability to rapidly optimise the structure so that production can commence at the earliest opportunity. As each part of the design is frozen, Aeromechanics can transition from design and optimisation to certification status models.
Bottom right: All systems integrated and flight tests begin. Flight tests are for flight not structural tests. Hence Aeromechanics must complete its structural justification prior to this event!
Bottom left: Pilots are always proud of their hi-tech sleek machines. The consequences of failure are the same whatever is being flown.
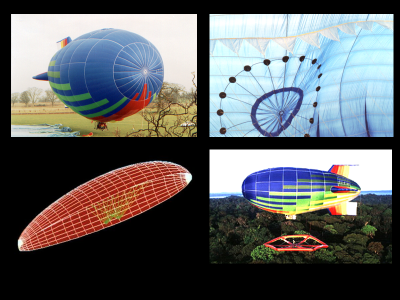
Designed the AS300 (300,000 cuft) hot air airship envelope and integral inflatable fins for Lindstrand Balloons Ltd. The envelope was shape optimised for minimum drag and improved positive control response from the tail compared to its sister ship the AS261. Catenary curtain design was optimised for maximum stability under thrust & pitch conditions and also minimum weight. Finite Element modelling and analysis was used extensively throughout the design.
Bottom left: A crude but powerful Finite Element Model for the optimisation of the catenary suspension design under multiple loading conditions.
Top left: Take-off for first test flight. Note the uniformity of the upper seams.
Top right: A view inside the envelope during inflation that emphasises the need for smooth transitional stiffness in the design to reduce stress concentrations.
Bottom right: The AS300 Hot Air Airship deployed over the tropical rainforest. The Airship would be inflated with hot air and the pneumatic raft attached. With several scientists riding in the gondola the pilot would fly to the desired location and land the scientists with the raft on the canopy. Several days later the pilot could re-inflate the airship to fly back to the same location and pick up the scientists and raft leaving no footprint evidence.